成形前の材料準備・・・裁断工程
こんにちは、スタッフKです。
10月に入ってようやく少しだけ涼しくなってきた感じもしますが、
先日もお伝えした通り弊社の工場内はまだまだ真夏状態です。
早く冬になってほしいものですね。
さて前回は加硫前のゴムについてお話をさせて頂きましたが、
今回も引き続きという事でやっていきましょう。
加硫前のゴムを加硫成形して、ゴム製品を作るためには製品の形状を彫った
鉄の塊、「金型」が必要になります。この金型に材料であるゴムを入れていくのですが、
製品や金型の形に合わせて材料は細かく裁断していかなければいけません。
屋台やお店で焼かれている「たいやき」の鉄板を見た事ありますでしょうか?
ゴム製品の金型もあのような感じで、製品の形状が彫り込んである所に
ゴム材料を入れ、挟んで熱をかけて成形をしていきます。
なので、大きなゴムシートそのままを入れる事は出来ませんので、
弊社では短冊形状に裁断した材料をよく使用しています。
ゴム材料を裁断するためには専用の裁断機を使用します。
ゴムの種類などによっても裁断機の仕様は変わったりするのですが・・・
弊社で使用しているのは「押し切り」と言われるギロチン形式の裁断機です。
これで全てのゴム材料を裁断しています。
縦横の幅をプログラムしてスイッチを押せば・・・後は自動で切断。
昔の裁断機はアナログだったのでこうはいきませんでしたが、現代の技術はすごいですね。
機械の寸法精度も1/1000まで設定出来ますから、非常に高精度です。
ただし加硫前のゴムのシートは厚み方向は凹凸が多少あり、
高精度で同じ幅で裁断したとしても1本辺りの重量には少々差が出ます。
この「重量管理」がゴムの成形では非常に重要な要素となってきます。
それはまた別の話・・・。
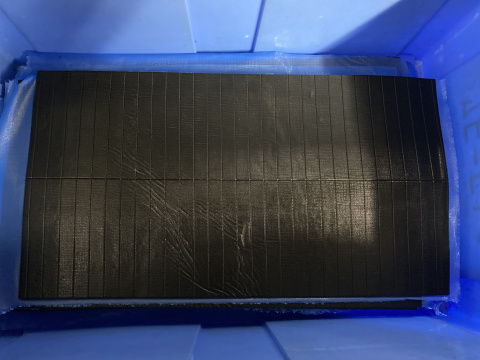
この材料、切込みは入っていますが実は微妙に繋がっています。
バラバラに切ってしまうと取り回しが悪く、整列させるのにかなり時間がかかってしまいます。
このようにちょっとだけ繋がっていれば、少し引っ張れば簡単に千切れますので
裁断後に改めて整列させる必要が無く、時間短縮に繋がります。
切った後の材料は成形するまでの間、冷えた場所で保管しておきます。
弊社の成形工程は1直・2直共に成形機を18台稼働していますが、裁断に関しては1台のみです。
同業さんと比較するとかなり少ない・・・かも?
この辺りは各社のやり方の違いや機械性能の差が出るところですね。
「切る」という分野においては弊社は別に特別なノウハウがあるわけではないのですが、
加硫前のゴムのように形状が不安定な物をキレイに切っていくというのは
それはそれで結構難しく、機械の性能に頼る事にはなるのですがどのようなやり方をしたら
うまく形状を保って切る事が出来るのかなど、設定項目は結構多かったりします。
特に今の新しい裁断機を導入してから、やれる幅は増えたのですが実際使いこなせて
いるのかというと・・・まだまだですね。
裁断の技術力ももっと向上させていきたいものです。
それではまた。
10月に入ってようやく少しだけ涼しくなってきた感じもしますが、
先日もお伝えした通り弊社の工場内はまだまだ真夏状態です。
早く冬になってほしいものですね。
さて前回は加硫前のゴムについてお話をさせて頂きましたが、
今回も引き続きという事でやっていきましょう。
加硫前のゴムを加硫成形して、ゴム製品を作るためには製品の形状を彫った
鉄の塊、「金型」が必要になります。この金型に材料であるゴムを入れていくのですが、
製品や金型の形に合わせて材料は細かく裁断していかなければいけません。
屋台やお店で焼かれている「たいやき」の鉄板を見た事ありますでしょうか?
ゴム製品の金型もあのような感じで、製品の形状が彫り込んである所に
ゴム材料を入れ、挟んで熱をかけて成形をしていきます。
なので、大きなゴムシートそのままを入れる事は出来ませんので、
弊社では短冊形状に裁断した材料をよく使用しています。
ゴム材料を裁断するためには専用の裁断機を使用します。
ゴムの種類などによっても裁断機の仕様は変わったりするのですが・・・
弊社で使用しているのは「押し切り」と言われるギロチン形式の裁断機です。
これで全てのゴム材料を裁断しています。
縦横の幅をプログラムしてスイッチを押せば・・・後は自動で切断。
昔の裁断機はアナログだったのでこうはいきませんでしたが、現代の技術はすごいですね。
機械の寸法精度も1/1000まで設定出来ますから、非常に高精度です。
ただし加硫前のゴムのシートは厚み方向は凹凸が多少あり、
高精度で同じ幅で裁断したとしても1本辺りの重量には少々差が出ます。
この「重量管理」がゴムの成形では非常に重要な要素となってきます。
それはまた別の話・・・。
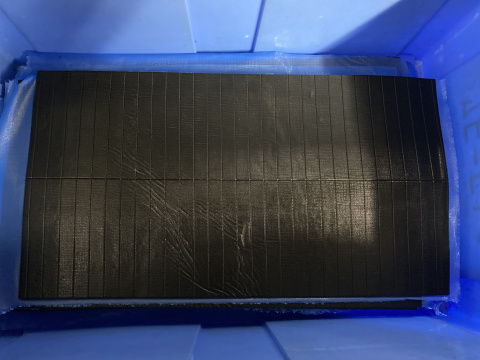
この材料、切込みは入っていますが実は微妙に繋がっています。
バラバラに切ってしまうと取り回しが悪く、整列させるのにかなり時間がかかってしまいます。
このようにちょっとだけ繋がっていれば、少し引っ張れば簡単に千切れますので
裁断後に改めて整列させる必要が無く、時間短縮に繋がります。
切った後の材料は成形するまでの間、冷えた場所で保管しておきます。
弊社の成形工程は1直・2直共に成形機を18台稼働していますが、裁断に関しては1台のみです。
同業さんと比較するとかなり少ない・・・かも?
この辺りは各社のやり方の違いや機械性能の差が出るところですね。
「切る」という分野においては弊社は別に特別なノウハウがあるわけではないのですが、
加硫前のゴムのように形状が不安定な物をキレイに切っていくというのは
それはそれで結構難しく、機械の性能に頼る事にはなるのですがどのようなやり方をしたら
うまく形状を保って切る事が出来るのかなど、設定項目は結構多かったりします。
特に今の新しい裁断機を導入してから、やれる幅は増えたのですが実際使いこなせて
いるのかというと・・・まだまだですね。
裁断の技術力ももっと向上させていきたいものです。
それではまた。
経営・工場|2022/10/18 Tue